ME undergraduate students gain real-world experience on projects that help industry, nonprofit, government and healthcare partners.
In the basement of the Mechanical Engineering Building one week before the ME Capstone Expo Fair, students put finishing touches on their senior design projects, also known as capstones.
During their last year in ME, undergraduate students pursue their technical and professional interests through capstones sponsored by industry, nonprofit, government and health-care partners. Other capstones this year focused on research in ME faculty labs and the Washington Clean Energy Testbeds, as well as projects within student organizations.
The quantity and fidelity of the prototypes at this year’s expo really speaks to the amount of progress they’ve made.”
ME recently revamped its capstone program to add more structure and guidance, including regular check-ins about milestones such as project definition and preliminary design reviews. The student teams decided on appropriate scopes for each milestone so they could complete their objectives by the end of the project. Students showcased their hard work during the second annual capstone fair, held on May 30.
“This is the first cohort of students going through our new capstone sequence,” says ME Capstone Director and Assistant Teaching Professor Eli Patten. “The quantity and fidelity of the prototypes at this year’s expo really speaks to the amount of progress they’ve made.”
Students may have a diversity of projects to choose from, but they all share the experience of going through a full-cycle design process, from defining the problem to prototype fabrication and testing.
Below, we highlight three capstone teams that made their brainstorming, research and sketches come to life in the form of a seaweed processing mechanical press, an adjustable platform for testing lift trucks and a medical device to help children in need of breathing assistance.
Seaweed solutions
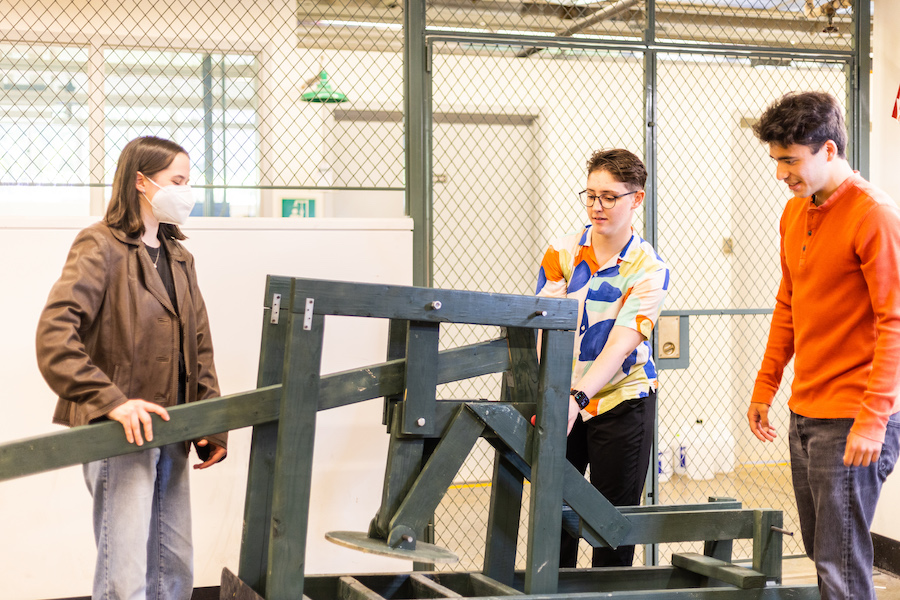
Students demonstrate how to use the mechanical press they created to help dry seaweed. Photo by Raymond Smith/UW Photo.
A partnership with Puget Sound Restoration Fund and Calm Cove Shellfish
Faculty adviser: ME Assistant Teaching Professor Eli Patten
Students: Courtney Avioli, Joe Condit, Emily D’Arcy, Jon Marstall, Edwin Miller
In the summer and amplified by climate change, excess Ulva seaweed grows in the Puget Sound and covers shellfish cultivation gear, becoming a burden for farms such as Calm Cove Shellfish in Shelton, Washington. The quickly growing seaweed can suffocate clams, oysters and other farmed shellfish. When it decomposes, the seaweed can negatively impact the local water quality.
The nonprofit Puget Sound Restoration Fund (PSRF) is developing experimental seaweed drying systems. However, wet seaweed is heavy, taking time and labor to transport. In collaboration with PSRF, a student capstone group developed a human-powered device that helps dry the seaweed so it can be more easily removed and used for different purposes such as compost material.
After creating 3D models of the device using computer-aided design (CAD), the team created the press using two-by-four lumber. To use the device, a long mechanical arm is pulled down, which applies pressure to a five-bar linkage, a mechanism they’d recently learned about in class that can expand or contract. This lowers a circular press that squeezes the water from a basket of wet seaweed, making the seaweed lighter and easier to transport.
“We created a press that maximizes the mechanical advantage,” says project member Courtney Avioli. “For example, we knew that having a longer lever arm would increase mechanical advantage and apply more force to the seaweed.”
The device, nicknamed “Arlo,” could remove more than 35% of water from the seaweed, if the structure were stronger and made out of more durable materials. The students presented their results to the shellfish farmers who had provided input throughout the process.
“The employees liked how it was easy to use and pressed out a decent amount of water,” team member Joe Condit says.
The students and project sponsors celebrated together with a picnic at the farm. As a final step, the students made recommendations for the next iteration of the device and created a manual that explains how farmers can construct the affordable and accessible design themselves.
“I like how the project is community-based and solves a real problem,” says team member Emily D’Arcy. “This isn’t a project that will just be filed away.”
The students were recognized for their work with the 2023 Outstanding Design Award at the ME graduation ceremony.
Adjustable height test load tower
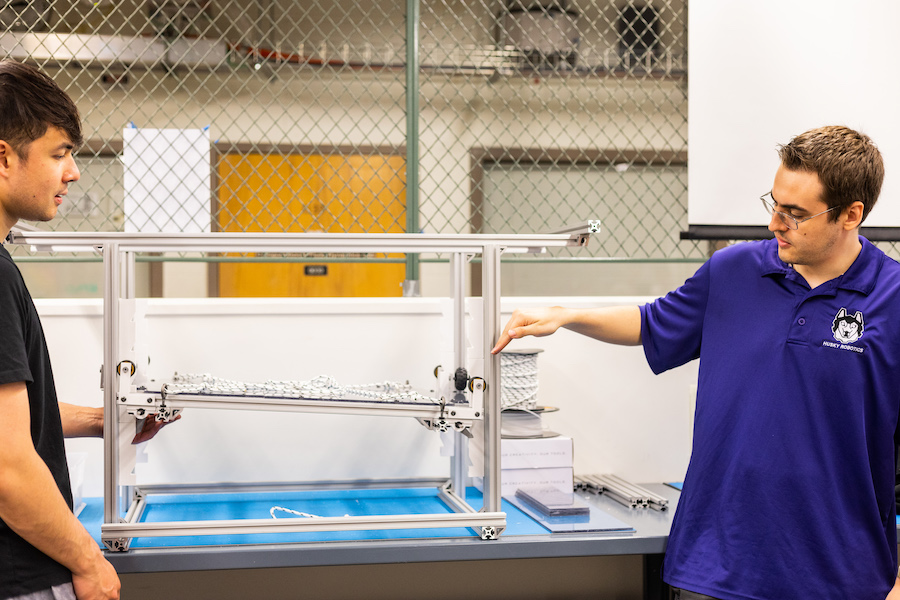
Zach Oropesa and Jordan Smith showcase their scale model of an adjustable test load tower. Photo by Raymond Smith/UW Photo.
A partnership with Hyster-Yale
Faculty supervisor: ME Assistant Teaching Professor Eli Patten
Students: Zachary Chilian, Kailey Diaz, Zach Oropesa, Jordan Smith
Hyster-Yale Group is a company that manufactures lift trucks, which are used for raising and carrying heavy materials. To test and validate critical structural components and truck functions, the company runs instrumented trucks on test courses that include moving loads on and off elevated platforms. The platforms – static steel structures that are time-consuming and expensive to build – are non-adjustable, so employees must use different structures to accurately test lift trucks with different lift height capabilities.
Looking for a more efficient way to achieve unique platform heights for specific tests without stacking or creating new fixed height towers, the company tasked an ME student capstone team with finding a solution.
“We worked with Eli and our industry contacts at Hyster-Yale to come up with different ideas for the design,” says team member Jordan Smith. “After sketching and 3D modeling, we created a scale model.”
The team of students successfully designed a platform for a test load tower that can quickly adjust in height from two to five meters, or about six-and-a-half to 16.4 feet. The full-scale model can hold 11,023 pounds. They also constructed a scale model of their design to demonstrate how it works.
When designing the prototype, the students considered safety, reliability and ease of operation. They then cut each piece of aluminum and 3D-printed plastic to size in the ME machine shop. Wheels on each side of the platform keep the load surface-level while it is raised. When the platform gets to the top, a spring resets it so the platform can be lowered. The students used skills they learned in class to design the spring and calculate how the structure would perform under different real-world conditions.
“It was rewarding to see our design that started on paper come to fruition and become a scale model,” says team member Zach Oropesa.
SmarTrach
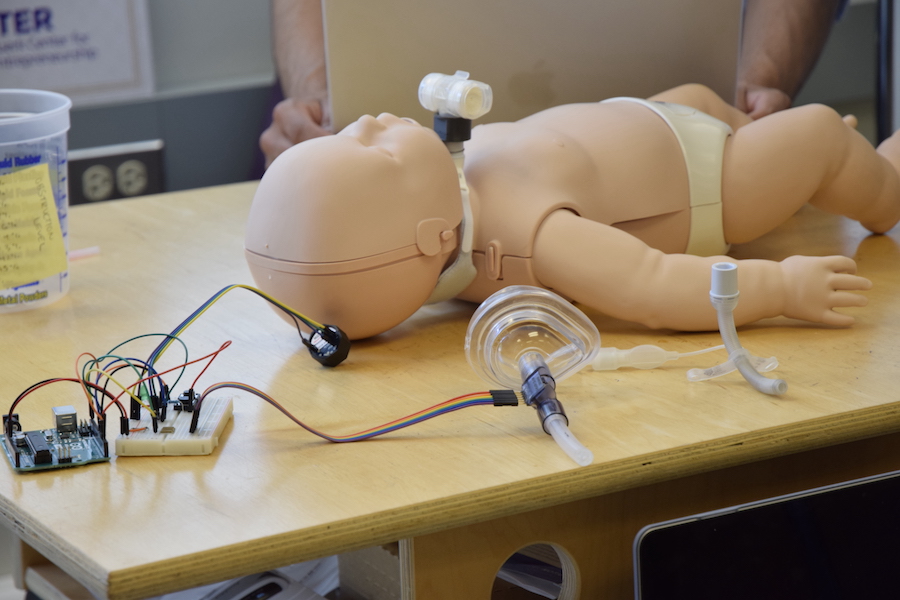
Students demonstrate how SmarTrach, a device that monitors a tracheostomy tube, works on an infant mannequin. Photo by Eli Patten.
A partnership with Engineering in Health Innovation (EIH) and Seattle Children’s
Faculty adviser: Soyoung Kang, Clary Family Early Career Development Professor in Engineering Innovation in Health
Students: Hans Erickson, Dylan Heino, Vamsi Jonnalagadda, Clara Tamura
A child who needs help breathing might undergo a tracheostomy, a procedure that creates a small hole in the front of the neck and the windpipe. A small tube is placed into the opening and connects to a manual airbag or breathing machine. This enables the child to breathe through the tube, which they may need from months to years.
When the child returns home, a nurse or caretaker stays with them in case mucus needs to be removed from the tracheostomy tube so it doesn’t prevent them from breathing.
However, there isn’t currently an efficient way to identify when the tube is blocked. SmarTrach, an ME capstone project and Engineering Innovation in Health (EIH) collaboration, is developing a device that wirelessly monitors a tracheostomy tube and can detect blockage. An alarm sounds when air obstruction reaches intermediate or emergency levels.
The team began their preliminary work in fall 2022. “We did a deep-dive into clinical research to understand the problem and how it affects patients, parents, clinicians and hospitals,” says team member Dylan Heino.
After talking with clinicians, the team decided that measuring airflow using a hot-wire airflow sensor – instead of acoustics or vibration – was the most direct way of identifying tube blockage. They attached the sensor externally to the tracheostomy tube instead of modifying the tube’s design, which could potentially add obstruction and would need additional FDA approvals.
They tested the sensor in tubes with artificial levels of obstruction while someone breathed into a connected CPR mask. Using straws containing different materials – such as toothpaste, pipe cleaners and hot glue – they measured how well the device detected different levels of blockage.
To collect data about how the obstruction changed airflow, the team developed a specialized algorithm. “We didn’t have coding experience, so we had to learn how to write code to implement it into our device,” says team member Clara Tamura. “It involved lots of trial and error.”
They worked with one of their mentors, Andrew Davidson, associate teaching professor in Human Centered Design & Engineering, to implement their code and include a button, triggers and an alarm into the tiny device.
In addition to creating the device, the students learned about the process of commercializing medical devices. They became familiar with FDA regulations, created a five-year financial plan and estimated manufacturing costs. At the 2023 Hollomon Health Challenge, the students were recognized for their work with the Best Idea Prize for patient safety.
Have an idea for a capstone project?
Visit Industry Capstone Program to learn more about how to partner with us!
Originally published August 17, 2023