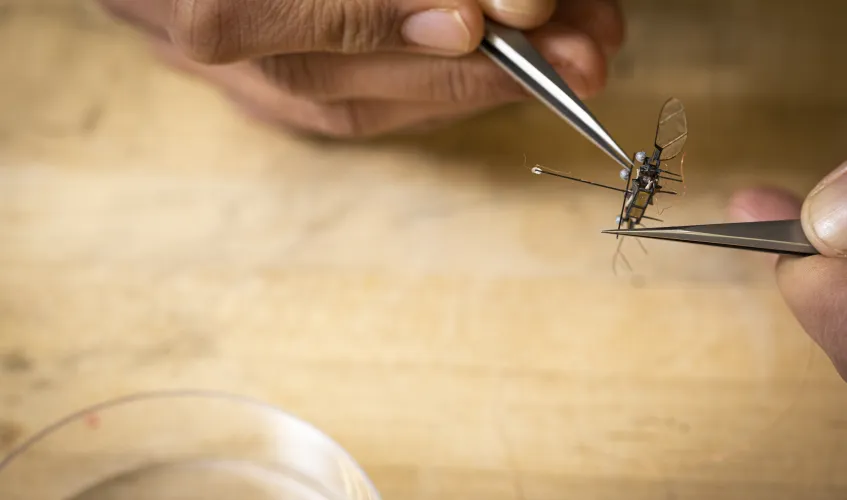
ME researchers in the Autonomous Insect Robotics Laboratory are developing insect-sized flying robots for tasks such as surveying crop growth and detecting gas leaks. Photo by Mark Stone
The emerging discipline of nano-engineering is uncovering countless possibilities for advancements in manufacturing, robotics, health care, energy and other industries by revolutionizing materials, structures and systems at the smallest scale.
But how small is small? Nano-engineering is the manipulation of materials and processes at the nanoscale, which is about one to 100 nanometers. (For reference, a human hair is about 80,000 to 100,000 nanometers wide.) At the UW, much of this research takes place through the Institute for Nano-Engineered Systems (NanoES).
Applying individual nano-elements to large-scale systems is one of the field’s biggest challenges. Doing so often requires a multidisciplinary approach to systems engineering and problem-solving — a skillset with which mechanical engineers are well-equipped. Currently four ME faculty are part of the NanoES community of researchers. Whether they are developing new materials and structures, creating bio-inspired miniature robots or assessing how nanoparticles impact human health, our faculty are helping to shape this research frontier. We highlight a few of their projects here.
Assessing health impacts of nanoparticles
Exposure to nanoparticles present in air pollution — from traffic emissions, forest fires and manufacturing processes — can result in health problems including cardiopulmonary diseases and cancer. The toxic potential of these particles depends on their size, structure and chemical composition. To evaluate the chemical composition of combustion nanoparticles and the health impact of their nanostructures, The Novosselov Research Group led by ME research associate professor Igor Novosselov is developing new techniques.
For example, molecular engineering doctoral student Justin Davis has developed an analysis technique tracking the evolution of particle nanostructures during their formation, finding that young, amorphous particles show more of an increased toxicological response than structured, mature particles. And ME doctoral students Gaurav Mahamuni and Jay Rutherford have developed a novel method using excitation-emission matrix (EEM) fluorescent spectroscopy to analyze organic compounds associated with combustion generated particles. In combination with machine learning, the EEM analysis can be used to evaluate nanoparticle toxicity and in the development of wearable sensors to monitor and assess exposure to harmful particles.
Developing integrated functional materials
Wearable electronics are one example of a real-world application that benefits from nanomaterial innovation. Whether they are directly attached on skin as seen here or integrated in clothes, these electronics collect data to monitor human health and activity. Image courtesy of Mohammad Malakooti
For innovative nanomaterials to be used efficiently in the real world, they must be reliable, consistent and stable under all working conditions. They also need to be manufactured in a scalable and cost-effective way. To develop new functional materials that match the adaptability, multi-functionality and intelligence of natural materials, ME assistant professor Mohammad Malakooti is leading a research program that bridges the gap between nanoscale engineering and macroscale electronics and intelligent systems.
Nano-engineered materials — “nanomaterials” — can be designed to provide enhanced properties, including biochemical sensitivity, strength, selective transport, thermal or electrical conductivity and optical properties, to name a few. These types of specialized properties can improve the performance of many products and processes.
Researchers in the Malakooti Research Lab are studying scalable materials synthesis and integration, controlled stability of materials at the nanoscale, and versatile manufacturing of functional nanomaterials that are durable and long-lasting under real-world conditions. Their work within these areas will impact emerging applications, such as self-powered wearable electronics, printed electronic skin, multifunctional composites, integrated nanoscale devices and stretchable biosensors, among other products and devices.
Introducing insect-sized robots
Creating insect-sized robots involves challenges at most all levels of development, from operating the robots’ tiny wings to overcoming limits in the amount of computation needed to power them. Photo by Mark Stone
Insect-sized flying robots, such as those in development in the Autonomous Insect Robotics Laboratory (AIR Lab) can help with time-consuming tasks like surveying crop growth on large farms or detecting gas leaks. These robots soar by fluttering tiny wings because they are too small to use propellers, like those on larger drones. In addition to being able to easily maneuver tight places that are inaccessible to bigger robots, these robots also cost less to build.
However, creating insect-sized robots involves challenges at most all levels of development — from operating the robots’ tiny wings to overcoming limits in the amount of computation needed to power them. ME assistant professor Sawyer Fuller, who leads the AIR Lab, is looking to nature — particularly, to the sensory-motor control systems of biological insects — to solve these challenges. Insects perform tasks that remain at the forefront of robotic capabilities, such as landing on flowers buffeted by turbulent wind or performing maneuvers to dodge flyswatters.
Fuller’s team is developing robots with similar capabilities that are the size of bumblebees or smaller. They implemented the first integrated high-voltage electronics circuitry to power the robots’ flight, enabled rapid flight maneuvers using a tail-like appendage, and developed a new design with four wings for better control. The team’s advancements extend beyond insect robots to any area in which there is a need for miniaturized, power-efficient sensing and control systems or more dynamic, life-like robots.
Using nanoarchitecture to create better materials
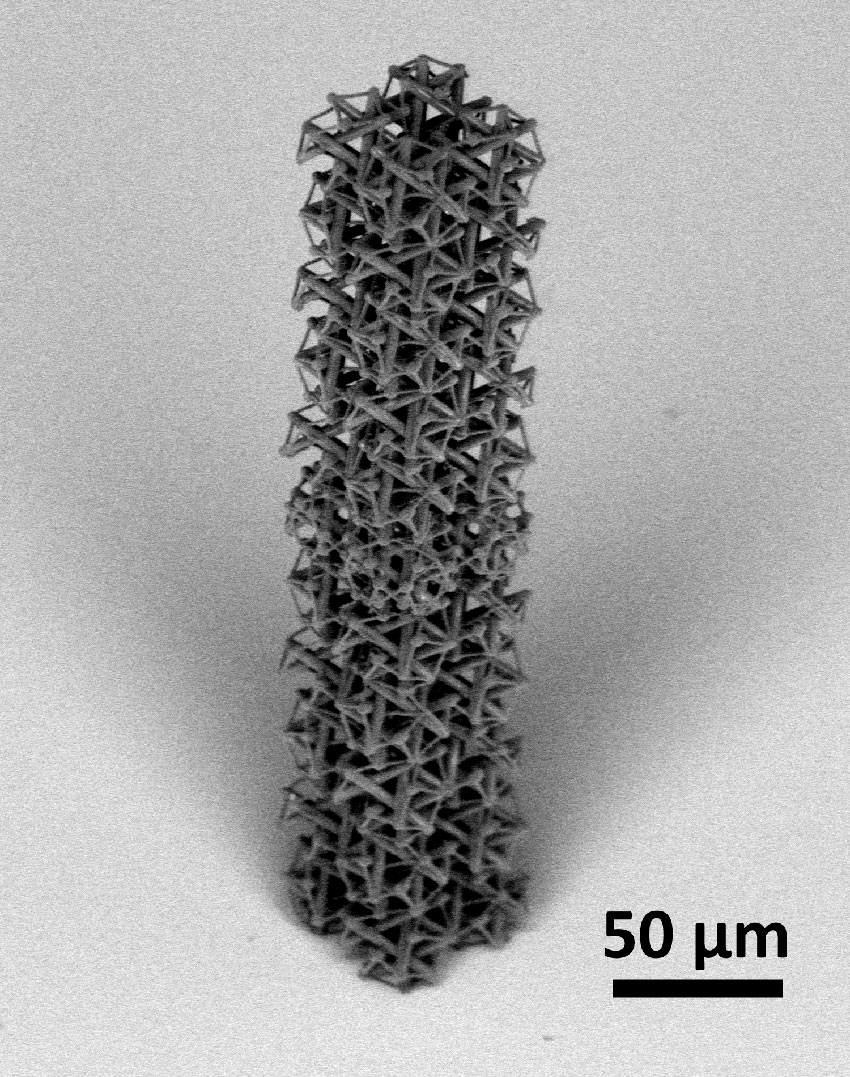
A two-photon lithography tetrakaidecahedron tensegrity tower, made in the Washington Nanofabrication Facility and imaged in the UW Molecular Analysis Facility by Caelan Wisont.
Nanomaterials have exceptional properties — strength, toughness, damage tolerance and enhanced ductility to name a few — often not found in traditional engineering materials. ME assistant professor Lucas Meza, who leads the Meza Research Group, is working to create novel nano-engineered materials by investigating the interplay between mechanics and architecture at the nanoscale.
Meza’s team combines nanoscale additive manufacturing with advanced materials processing techniques to create new materials from the nanoscale up. They also use in-situ nanomechanical testing to break down materials and study their properties at the nanometer level.
One of the group’s current projects is to create nanoscale tensegrity materials. Tensegrities are structures that obtain their integrity through tension networks. They are common in nature — in cell cytoskeletons, spider silk, musculoskeletal systems and other areas where strength and versatility are required. Traditionally tensegrities are developed at the macroscale by hand tightening rod and cable networks. Meza’s group uses nanoscale additive manufacturing to develop nanostructured rod and cable networks that are then thermally decomposed to create strong, carbon tensegrity-based artificial materials known as “metamaterials.” These metamaterials may one day be used as high-strength, shape-changing nanostructures and as scaffolding in artificial tissues.
Learn more about nano-engineering research at the UW
Originally published January 27, 2020