By Lyra Fontaine
ME researchers will work on projects funded by the U.S. Department of Energy that could improve the manufacturing of composites and electric vehicle batteries.
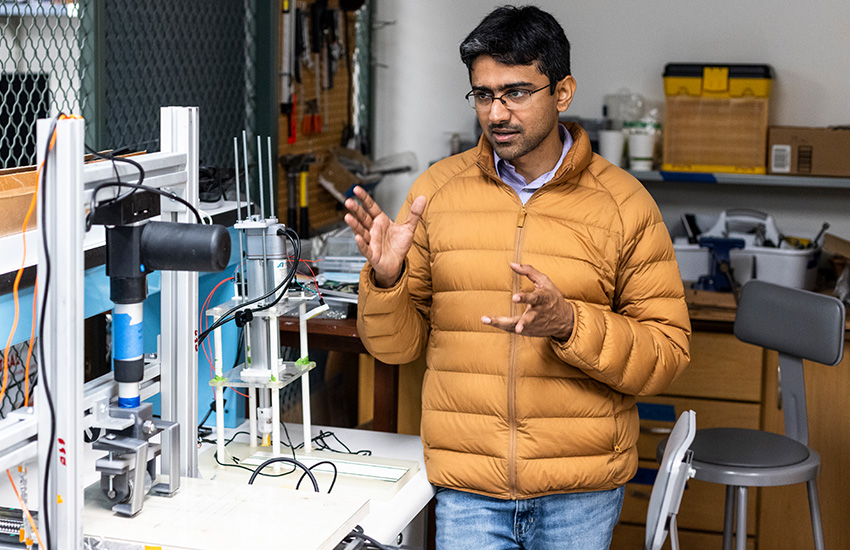
Assistant Professor Aniruddh Vashisth next to two automated welding platforms where his lab tests how radio frequency fields can heat and weld composite materials. Photo by Dennis Wise/University of Washington
The U.S. Department of Energy (DOE)’s Office of Energy Efficiency and Renewable Energy recently selected two projects for funding — led by or involving ME researchers — that will accelerate clean energy solutions for manufacturing in the United States.
The funding for both projects is approximately $6.26 million. The projects draw on the department’s expertise in advancing next-generation materials and developing technologies that accelerate energy efficiency.
The first project, which received approximately $1.8 million in funding, will contribute to the aerospace industry’s need for aircraft manufacturing technologies with improved energy efficiency. Assistant Professor Aniruddh Vashisth is the lead researcher on the project, which aims to use machine learning and radio frequency fields to weld industry-standard composites — lightweight, high-performance materials that are used to build aircraft, cars, windmills and more. Collaborators include Associate Professor Ashis Banerjee and Oak Ridge National Laboratory researcher Vipin Kumar. The team also includes researchers and engineers from the Institute for Advanced Composites Manufacturing Innovation (IACMI), Boeing, Electroimpact and Hexcel.
After five years of researching rapid manufacturing of composites using radio frequency fields, Vashisth is excited to further his work with support from the DOE.
“This work was accelerated by the UW’s location in Washington state, which is a leader in composites,” he says. “It’s wonderful to have this project funded and I’m grateful that my colleagues and collaborators believed in the idea.”
The second project, led by Pacific Northwest National Laboratory (PNNL), focuses on an innovative approach to manufacturing improved materials for electric vehicle batteries. Professor John Kramlich is a collaborator on the project, which received approximately $4.46 million. Other UW collaborators include Eleftheria Roumeli, an assistant professor in materials science and engineering (MSE), and Jun Liu, a professor in MSE and chemical engineering who holds the Washington Research Foundation Innovation Chair in Clean Energy. The researchers’ goal is to develop a technology for manufacturing single crystal nickel-rich cathode materials. The technology will improve facilities for single crystal production, simplify the manufacturing process and reduce costs.
“This project is an exciting challenge of trying to make a promising technology grow into a practical, commercial contender,” Kramlich says. “The interface between science and engineering has always been a very exciting place to be, and this project has all the ingredients: solid, fundamental science; the engineering challenges of scale-up; and the potential for a large economic and societal impact if successful.”
An energy-efficient way to manufacture composites
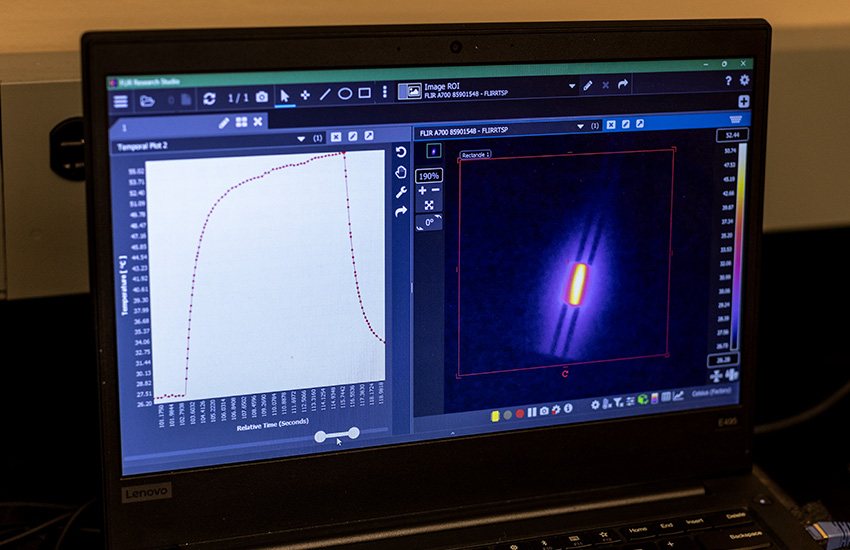
Thermal measurements using Forward Looking InfraRed (FLIR) technology show the rapid temperature increase achieved for energy-efficient heating of aerospace composites. Photo by Dennis Wise/University of Washington
Currently, robotic automated fiber placement machines create composite materials using an energy-intensive ion lamp that heats carbon fibers and deposits the materials in layers. Vashisth’s vision is to replace the ion bulb in these machines with a radio frequency applicator.
As a postdoctoral researcher at Texas A&M University, Vashisth learned that electric fields in the radio frequency range can be used to heat carbon nanomaterials. He wondered if, similar to how microwaves can quickly heat food, radio waves could rapidly heat materials in a controlled way and thus contribute to ultrafast manufacturing.
Since he joined the UW, Vashisth’s Composite Materials & Manufacturing Lab has discovered that it’s possible to rapidly cure and weld carbon fiber composite materials using heat from radio frequency fields. They’ve written papers and secured patents on this technology with applications ranging from welding and curing composites to chemical synthesis using radio frequency fields.
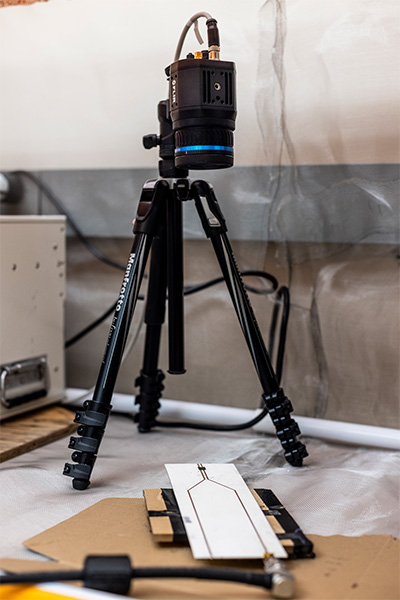
Vashisth’s lab found that it’s possible to rapidly cure and weld carbon fiber composite materials using heat from radio frequency fields. Shown here is a FLIR camera looking at the radio frequency applicator “wand” with two parallel copper traces that emit strong electromagnetic fields that rapidly heat carbonaceous materials. Photo by Dennis Wise/University of Washington
With the help of an automated machine, the researchers move a wand-like radio frequency applicator close to a carbon fiber material to heat it.
“One of the nice things about radio frequency heating is that it is non-contact, so the radio frequency wand does not need to touch the target materials,” Vashisth said.
The team recently found that radio frequency fields can rapidly heat some carbon fiber composites up to 800 degrees Celsius in one second.
Using these findings, Vashisth hopes to robotically weld composites using radio frequencies with the DOE funding. First, the team will conduct experiments and simulations that describe how relevant materials respond to radio frequency heating. They will then use machine learning, with the help of Banerjee’s expertise, to inform optimal processing conditions. Lastly, the team will develop a robotic system that can intelligently and quickly weld thermoplastic composites together. Kumar’s lab at Oak Ridge will help scale the technology.
If it’s successful, the robotic system would lead to 15 percent faster welding and reduced environmental impact, while maintaining or improving the composites’ mechanical properties.
Better battery performance in electric vehicles
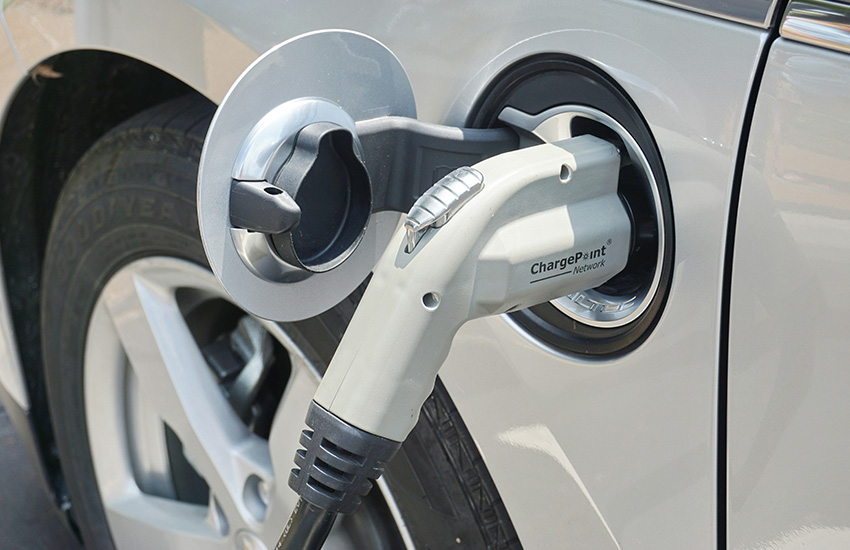
Photo by Robert Linder via Unsplash
According to the U.S. Environmental Protection Agency, people are increasingly buying cars that operate on alternative fuels, such as electric vehicles, which create no tailpipe emissions. However, one obstacle to the broader adoption of electric vehicles is the limitations on the batteries’ number of charging cycles.
With its high energy density and rechargeability, lithium-ion batteries are found in everyday items such as laptops and cell phones, as well as electric vehicles. Over time, they can fail and no longer hold a charge. One reason for the batteries’ performance loss is in the current materials used in the cathode, the part of the battery where electrons move to and from. The most common materials are composed of aggregates of small crystals joined at grain boundaries. Most problems with lithium-ion batteries, such as generating gas and cracking, occur at these grain boundaries.
A promising cathode alternative is nickel-rich transition metal oxides, which have potential to provide a high energy density and a low-cost solution. Because they are made up of a single crystal instead of many crystal grains with grain boundaries, nickel-rich transition metal oxides could improve upon current electric vehicle battery performance. Though manufacturing single crystals is challenging, PNNL researchers have discovered a significantly simpler way of creating single crystals that reduces the number of manufacturing steps by about two-thirds.
This method will inform the DOE-funded project. The researchers will work on designing a drop-in process in which the new single-crystal manufacturing process can fit into an existing manufacturing facility, which would lower costs.
“This project identifies and addresses the scientific challenges behind scaling up the manufacture of these promising cathode materials,” Kramlich says. “We are seeking a cost-effective route that bridges the knowledge gap between academic research and industry manufacturing.”
Originally published January 24, 2024